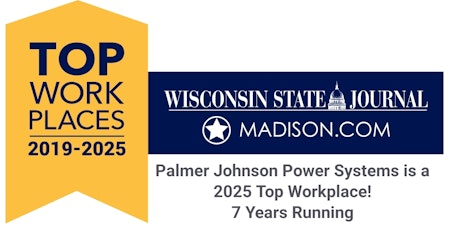
5 Tips to Extend the Life of Your Hydraulic Pump Drive

Hydraulic pump drives are an essential component in a wide array of equipment, connecting the prime mover to hydraulic pumps. Pump drives are utilized across many industries, such as oil & gas, agriculture, construction, forestry, and mining. We know how critical uptime is to success in those industries. That's why we've put together our top 5 tips to maximize the life of your hydraulic pump drives and how you can keep it running for years to come.
⭐ TIP #1: PROPER OIL LEVELS & OIL WEIGHT
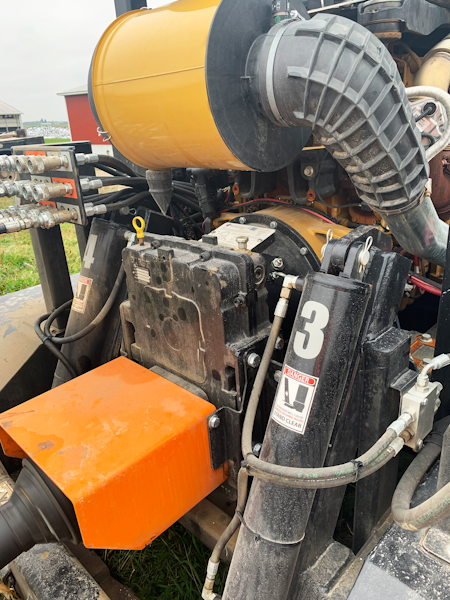
The most common reason for a hydraulic pump drive failure is that there is not enough oil or no oil at all. It may seem outrageous to think that someone would run a pump drive with no oil, but we see it all the time. If this happens, the internal gears and shaft will get eaten up, and you will be looking at a hefty repair bill.
It is best practice to check the oil level before daily operation and fill it as needed. Along with ensuring there is oil in the pump drive, it is essential to use the recommended weight of oil for the temperature range you are operating at. You will find the recommended oil weight in the service manual of your pump drive.
⭐ TIP #2: PROPER MAINTENANCE
In addition to ensuring your pump drive has the correct oil level, performing daily maintenance can go a long way to keeping your pump drive working properly along with catching small issues before they become large ones. The pump drive should be inspected daily for signs of leakage. It’s also a good process to allow the pump drive to warm up prior to operation. This warm up period allows the lubrication to thin out a bit and get to all important points before applying the load.
⭐ TIP #3: PROPERLY TRAINED OPERATORS
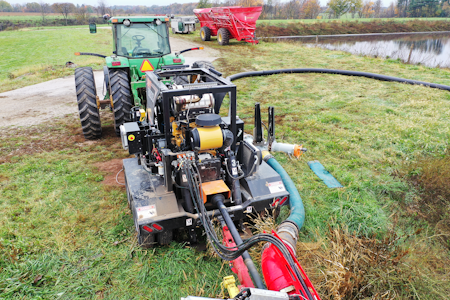
Most pump drive failures result from operator error or poor maintenance mistakes. Therefore, if you own and operate the machinery yourself, it’s crucial to ensure that you are trained on how the pump drive works and routine maintenance. A quick read through your Pump Drive's service manual will often explain how the unit works, which reduces operator errors that cause premature failure.
If someone else will be operating the machinery, ensure that they are adequately trained on that pump drive and perform daily maintenance. If you have multiple operators on your staff, I recommend teaching good operational practices and implementing a good maintenance program. These will help maximize the life out of your pump drives and the other components on your machinery.
⭐ TIP #4: UPGRADE TO A TORSIONAL INPUT COUPLING
We commonly see failures happen at the input. There are several reasons why this can occur, but the most common cause is due to excess vibrations coming off of the engine. This issue is seen more commonly with larger engines and applications.
If you are experiencing premature failure with a standard flex plate, we recommend running a torsional vibration analysis (TVA) on your application. Running a TVA will require the engine and hydraulic pump details. Once the TVA is complete, we can offer an upgraded torsional input coupling which will help limit the effects of vibration from the engine, which will ultimately help to eliminate these input failures and keep you up and running longer. We presently supply couplings from Reich and Torsion Control Products (TCP) to be used with hydraulic pump drives.
⭐ TIP #5: PAY CLOSE ATTENTION TO THE INPUT
Each Pump Drive input style has specific tips to ensure proper operation. Good operation techniques are key to having a long life from a clutch.
⚙️ CLUTCHED INPUT
The clutched input pump drives have more moving pieces and require additional tips. First off, new clutch plates have a “wear-in” period. New clutch assemblies are also not properly adjusted from the factory.
So you will need to adjust the pump drive when it is first run. Then you will check the clutch adjustment daily until it’s properly adjusted. From there, we recommend checking the clutch adjustment every week after the initial wear-in. Next, lubricate the throw out bearing once a day with a small amount of grease while ensuring not to over-grease the clutch. Over-greasing the clutch can result in a grease build-up within the bell housing, eventually making its way to the friction plates, ultimately making the clutch fail.
4 CLUTCH OPERATION TIPS:
- Always engage a clutch at idle.
- Bumping the clutch to get the load going before full engagement can help ease the stress on the clutch plates.
- Engagements are added stress on the clutch. Therefore, any operational practices you can put into place to reduce the number of clutch engagements can extend the life of the clutch.
- The hand lever should always be as close to vertical as possible when engaged to avoid putting thrust on the throw out bearing.
⚙️ REMOTE INPUT
Proper alignment of the drive shaft is essential, along with making sure your driveline is properly balanced can ensure there is no additional stress on the remote input assembly. Additionally, there must be no or minimal side load for most remote input pump drives.
⚙️ PLATE INPUT
Plate inputs are generally trouble-free. However, during installation, the flywheel tolerances should be checked. In addition, the flywheel should be clean and free of any dirt or corrosion that can throw off alignment.
PALMER JOHNSON IS YOUR PUMP DRIVE EXPERT
Thanks for reading and make sure to check out our other pump drive blogs to help maximize what you get out of your equipment. Make Palmer Johnson your first call for all of your pump drive needs. Whether you are needing parts support, a replacement pump drive, a new application pump drive, or technical assistance, we’ve got the knowledgeable staff and industry-leading inventory to provide you with the best possible pump drive support.
Keep Reading
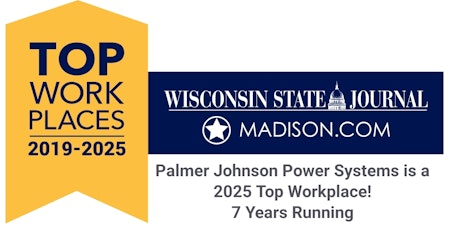